Sealcoating is a cost effective way to protect your asphalt pavement investment. It provides a dark black look to faded asphalt and smooths out small cracks and rough areas.
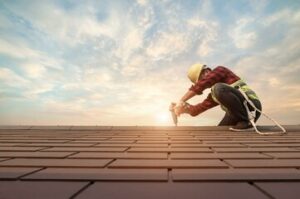
This is done by applying a coating of a mixture that contains sand, bitumen (or oil), and specific asphalt binder oils. This helps to replenish the degraded petroleum binder and oils. Visit https://www.rochesternysealcoating.com/ to learn more.
The PAHs from coal tar-based sealcoat can seep into the groundwater supply and enter lakes, rivers and streams or wash off the pavement into stormwater runoff. As a result, the toxic chemicals can kill fish, insects, amphibians and mammals. The PAHs are also photoactivated, which means they intensify their toxicity when exposed to sunlight. Runoff from coal-tar-sealed pavement has been shown to be very toxic to aquatic life even long after the sealcoat is applied and dries, according to research conducted by the Geological Survey. For example, the study found that minnows and water fleas exposed to coal tar runoff experienced 100 percent mortality up to 42 days after exposure.
While manufacturers of coal tar-based sealcoat will sometimes claim that their product is safe and will not contaminate other areas as long as it is given 24 to 48 hours to cure, this simply isn’t true. The chemical particles and fumes released by the coating during this time can be blown around by wind, stick to tires and car doors, and make their way into waterways, lakes and surrounding soil and air.
You can test whether your sealcoat is made of coal tar or asphalt emulsion by scraping a small amount of the material from your pavement and mixing it with paint thinner or mineral spirits. If the resulting solution looks like coffee, it is most likely made of asphalt emulsion and is safer for the environment.
Asphalt Emulsion
Asphalt emulsion is an environmentally friendly and cost effective alternative to coal tar sealcoating. It is used to reseal asphalt pavement, typically parking lots and neighborhood streets. Fresh asphalt emulsion can help prevent environmental damage from water, sun and ice as well as people-caused damages such as divots and pinholes.
Emulsions are made by dispersing asphalt into water through an emulsifying agent or surfactant. The emulsifying agent is a large molecule that has an electrically charged head soluble in water and a hydrocarbon tail soluble in asphalt. The emulsifying agent creates a stable structure around the bitumen particles that repels other molecules and keeps them suspended in water.
There are a variety of asphalt emulsions available that have different properties to suit specific applications. Some are designed to set quickly while others are slow set and are commonly used in spray application methods. They also come in various temperatures depending on their intended use.
Other additives can be added to asphalt emulsion for additional benefits such as wetting, leveling and flowing agents. These additives can improve the consistency and workability of the emulsion which is important for proper application. They can also reduce surface flaws such as craters, fisheyes and orange peel in the final coat of the sealcoat.
It is important to note that all emulsions will eventually break and revert back to asphalt and water. Some emulsions break by chemical destabilization and evaporation of the surfactant while others will break by a combination of both. These breaks are usually controlled by the addition of emulsion stabilizers which can extend their working life up to 100 times longer than without them. The storage and handling of asphalt emulsion is critical to its preservation until it can be applied.
Oil Based
Oil based sealers are a time-tested and effective way to protect asphalt surfaces from weather, traffic, and other environmental factors. When properly applied by a qualified asphalt contractor, this type of sealcoat can provide long-lasting protection and enhance the appearance of a parking lot.
One of the main benefits of using an oil-based sealer is that it provides a rich, glossy black finish that helps to improve the aesthetics of the pavement surface. This can help to increase the overall curb appeal of a commercial property and can be an excellent way to enhance the value of the property.
Another benefit of using an oil-based sealer is its superior durability. Oil-based sealers can typically last four to six years, which is significantly longer than the lifespan of many water-based sealers. This long-term longevity makes it an excellent choice for property owners who want to maximize the lifespan of their asphalt surface.
One drawback of oil-based sealers is that they require more extensive preparation and cleanup than their water-based counterparts. This can include pressure washing the parking lot to remove dirt, mud, and other debris. It is also important to ensure that the surface is free of cracks and potholes before applying the sealant.
Finally, oil-based sealers can produce a strong odor that may be difficult to deal with during the application process. However, this is a small price to pay for the exceptional protection and longevity that they offer.
Fast Dry
Asphalt sealcoating protects paved surfaces from the elements, prolonging their life and appearance. However, improper application or failure to follow the proper drying and curing procedure can reduce its effectiveness and lifespan.
Several factors affect how long it takes for a seal coat to dry and cure, so preparing for delays in your schedule is essential. The weather is the biggest factor, and ideal conditions speed up drying times.
Temperature, humidity, and sunlight are other important factors. Higher temperatures accelerate drying, while humid weather slows it down as moisture lingers in the air. Sunlight exposure expedites the drying process by promoting evaporation. Using fast-drying additives can also shorten drying time without affecting durability.
Avoid Premature Traffic
It’s a good idea to restrict vehicle and pedestrian traffic from the surface until it dries completely. Attempting to drive on a wet sealcoat can ruin its appearance and cause damage to the pavement. Sealcoat dries from the top down, creating a hard “crust” over a moist lower layer. Trying to force the coating to dry prematurely can result in cracking, staining, and other serious problems.
A professional paving contractor can offer valuable guidance regarding optimal curing conditions for your project. They can help you select a timeline that ensures proper drying and curing before traffic is allowed on the surface. They can also provide a range of high-quality asphalt maintenance products and expert application techniques, ensuring the best results for your property. Contact Asphalt Icons today for a quote! We use only the highest-quality materials and expert applications to create lasting, protective results for residential and commercial properties. We also offer detailed advice for post-application care to extend the longevity of your new asphalt driveway or parking lot.
Acrylic
Acrylic seal coats offer high-quality protection and restoration to asphalt pavement surfaces. They’re often breathable and available in a variety of sheens. They are a popular choice for driveways, tennis courts and shopping mall parking lots. However, due to their expensive price tag, they’re not a good option for larger areas of asphalt that receive heavy foot or vehicle traffic.
Acrylic can be either water-based or solvent based. It contains small particle solids suspended in a liquid carrier (water or solvent, such as xylene or acetone). Once applied to the slab, the liquid carrier dries and evaporates leaving the solid particles behind on the surface of the concrete to form the sealcoat. Water-based acrylics tend to be glossier and are more eco-friendly, whereas solvent-based acrylics darken the surface and have a lower sheen. Regardless of the type of acrylic you choose, make sure it’s rated for indoor or outdoor use.
Like all sealcoats, acrylic requires specific environmental conditions for proper application and adhesion to the pavement surface. If it’s applied in the wrong conditions, the sealcoat may flake off or peel. Additionally, acrylic can be affected by a wide range of chemicals and pollutants. It is recommended to only apply this sealcoat to dry surfaces that are free from oil, grease and other contaminants.
While the different types of sealcoats all provide protection to a variety of concrete surfaces, getting the most life out of your sealer depends on maintenance and recognizing when it’s time for rejuvenation or reapplication. Be sure to provide your workers with adequate PPE while applying a sealcoat, including coveralls and face masks to prevent exposure to harmful chemicals. International Enviroguard has a large selection of high-quality PPE to protect your workforce from on-the-job hazards.